HOME
|
|
PURWOX (USA), Inc.
C 1997
Technical Concept Analysis
The net product of the PURWOX process is a mixture of
primarily carbon monoxide and hydrogen with varying but smaller amounts of
methane, water and carbon dioxide. The gas has a net heating value of
around 300 BTU per standard cubic foot as produced. This type of gas is
commercially known as synthesis gas or syngas for short.
The process has some chemistry that has been proven
viable in similar type organics-gasification processes for producing
syngas over the last 70 years. Syngas is a basic building block for
several types of commercial processes. Ammonia-urea, methanol, synthetic
natural gas, hydrogen, several oxo-alcohols, and some synthetic motor
gasoline processes all start by generating some form of syngas. Most use
steam reforming and/or partial oxidation of natural gas (primarily
methane). A significant portion however, use other organic material,
mostly coal, though several projects using biomass and municipal solid
waste have also been funded and even commercialized to some extent.
Several plants have been started and successfully run
for several years. Some are still operating, especially in areas of the
world where indigenous oil and gas are rare but coal is plentiful. “Water
gas” production from the reaction of steam with coal or coke was the
principal means of providing municipal heating and lighting gas for the
first thirty years of this century. South Africa is an example where the
SASOL coal gasification complex has successfully supplied gasoline,
chemicals and synthetic natural gas to that nation for over 40 years.
Germany supplied much of its war needs in the 1940's from coal pyrolysis
and gasification. Dakota Gasification Co. has run a large 300 MW high
sulfur lignite gasification plant for several years in Beulah, North
Dakota. On a less spectacular scope, the Baltimore Municipal Waste
District ran a prototype trash gasification unit successfully, though it
was judged uneconomical in terms of energy production savings. This was
back in the late 1970's and early 1980's before eastern U.S. landfill
problems became a major environmental concern. Federal, state and
municipal governments and private investors have funded several similar
type of waste to product schemes since the early 1970's - again most being
viewed as alternative fuel plants.
Nearly all of these plants used some type of
free-oxygen based combustion internal to the gasification process. While
this can generate a great amount of heat inexpensively and reduce some of
the reactor space-time parameters, these design advantages are offset by
the need for more complicated environmental and safety control equipment.
Most of these syngas processes also require expensive oxygen-generation
and pressurized air-blowing equipment. The presence of free oxygen and its
direct waste-combustion products also present potential corrosive
situations that will complicate the process design.
PURWOX uses very high temperature steam and a high
temperature recycle stream to provide enough heat to drive the complete
gasification of all carbonaceous material leaving the reactor. In
addition, the bottoms materials of the reactor are in a molten metal phase
that can be recovered as a quality recycle material and molten slag that
is suitable for sale as clean building material or construction fill.
The process uses clean syngas (externally to the
reactor) to provide all necessary process heat and has approximately 50%
of the net gasifier to make gas available for sale or conversion into
steam, electrical power, etc. As an example, for a typical mid-size city
mix of municipal solid waste, a 10-ton/hr trash gasification facility
could support a 6-7 Megawatt (MW) power generation system.
The syngas product burns very cleanly in commercially
available power or steam generation equipment.
Potentially toxic agents found in trash (chlorine,
sulfur, fluorine, nitrogen, pesticides, batteries, heavy metals, etc.) are
reduced by the steam and hydrogen to a form that is readily removed and
recovered from the process gas product or in the liquid slag bottoms. The
high temperature gasification process breaks down the molecular structure
of the most chemically complicated feed material into very basic molecular
forms CO, H2, H20, CH4 and CO2. The lack of free oxygen in the process
stream eliminates the formation of dioxins, ketones, aldehydes, phenols
and other toxins characteristic of direct waste combustion or oxygen-blown
gasification processes.
Finally, the PURWOX process is amenable to mixed-type
organics processing. Adding various amounts of coal, used tires, spent
lube oil, coal tailings, petroleum-based insecticides or refinery waste,
medical waste, biomass, to a feed base of municipal solid waste (or one of
the other solids mentioned) is an exciting possibility. Very few
adjustments to the “garbage-gasification” process equipment would be
required to handle any type of above-mentioned wastes.
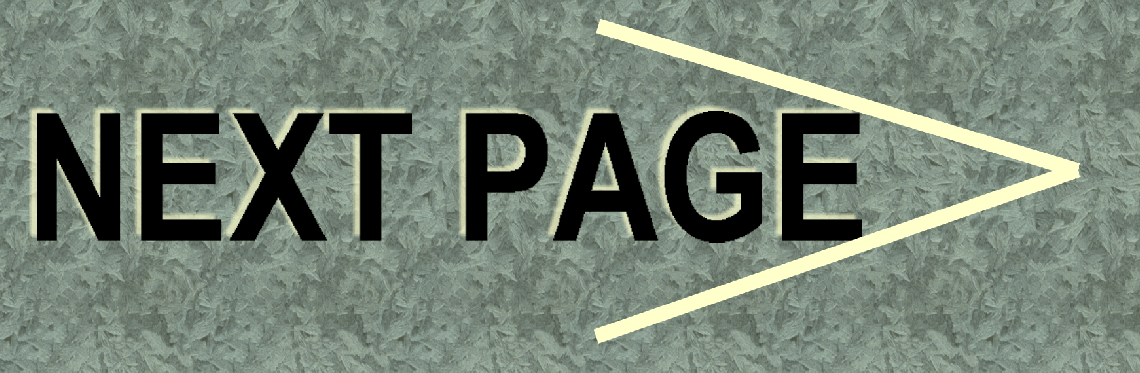
|