HOME |
|
PURWOX (USA), Inc.
C 1997
Recycled Gas
The recycle gas (removed at the top of the gasification
zone) and gaseous char gasification products flow upward through the
reactor providing the heat for thermal destruction of the organic waste
material in Zone II. The products this zone include volatiles, more
steam-reformation syngas, and hydrogenation products of cracked organic
chemicals such as alcohols, higher paraffins, a few organic oils and some
heavier hydrocarbons that are liquid at normal temperatures.
The inorganic molecular components of Chlorine,
Fluorine, Nitrogen, Sulfur and other wastes will form acid compounds such
as HCL, HF, NH3, H2S, etc. in this section, as long as free oxygen is
minimized inside the reactor. If not, all sorts of pollutants, such as NOx,
dioxins, aldehydes, ketones, etc. will be formed in unacceptable amounts.
The acid components are easily removed in downstream caustic-base
scrubbers. The others are not and have presented significant problems for
incineration-based waste removal processes for the last thirty years.
The pyrolysis gas is removed near the top of the
pyrolysis zone (Zone II) but the location may differ according to feed
type. From the pyrolysis offgas, known as pyrogas, heavier organic oils,
particulates, and other non-volatile pyrocompounds are removed (cyclone
separator) and returned to the gasification section of the converter. The
cyclone off gas is compressed and sent to a pressurized caustic scrubbing
system for removal of acid gas components. More organic liquid condensate
is recovered and recycled to the converter. The spent caustic, diluted
with condensed pyrogas water vapor, is flash evaporated and the water
vapor recycled as superheated makeup to the restorer gas stream. The
concentrated caustic sludge is pumped to the melt collection zone of the
reactor for encapsulation and fixation in the primarily alkali and
alkaline earth oxide molten slag material.
Above the pyrolysis zone, heat conduction from the
lower bed areas drives off all of the surface water associated with the
SOF, as well as substantial portion of that chemically bonded or adsorbed
inside the waste components. A bleed vent of primarily steam from the top
of this “drying zone” (Zone I) enhances removal of this gas without
removing significant portions of the pyrogas. It also provides a bit of
convective gas flow for converter temperature profile control.
Syngas Use
Clean pyrogas from the scrubber is used for three
purposes:
-
Fuel for fired heating (external to the reactor) of
the restorer gas and superheating recycle steam.
-
Product syngas for sale as a chemical feedstock or
as a feed gases for conventional power generation systems, either
steam driven or combustion-turbine driven.
-
Intermittent or as a continual bleed makeup for the
recirculating restorer gases. Converter control may dictate some
modification to the amount of pyrogas that is recycled to the restorer
gas stream.
Conversion of municipal solid waste energy
potential to product pyrogas heating value is about 75% with about half
of this product needed for fired combustion gas heaters to drive the
pyrolysis and gasification reactions.
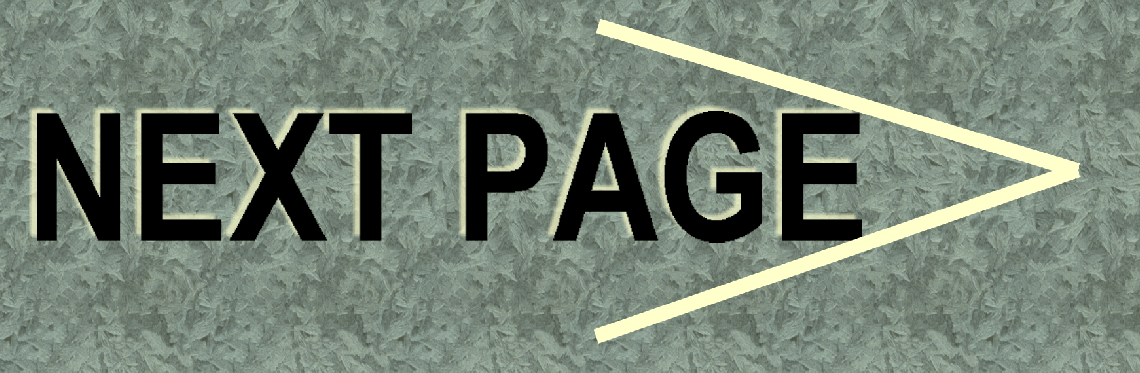
|